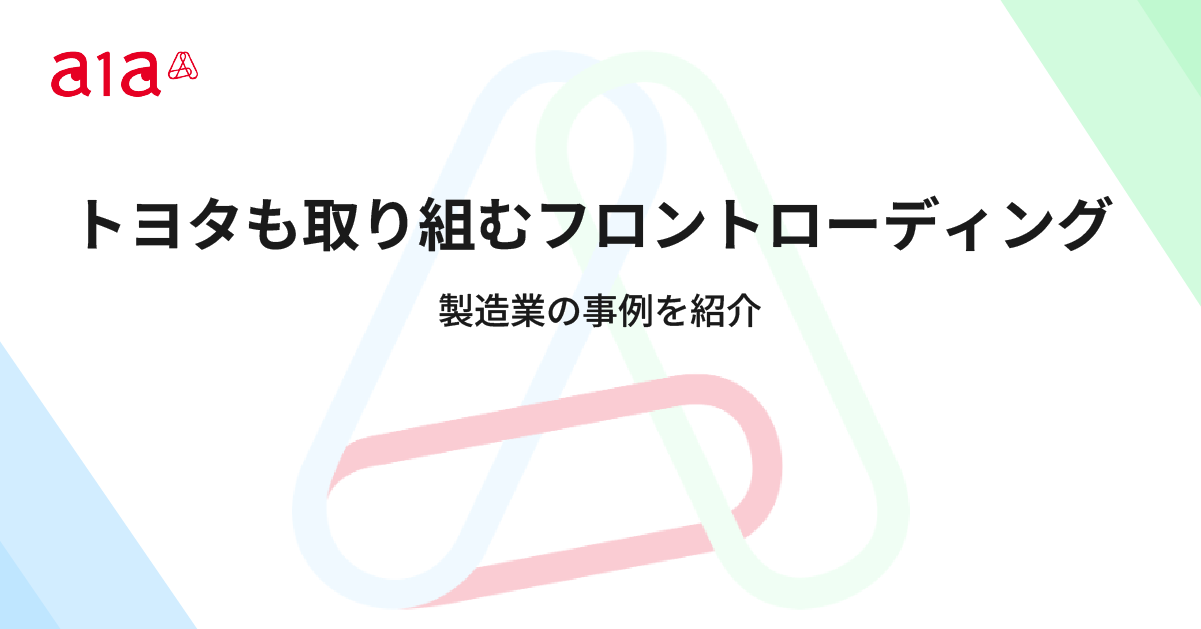
製造業では、設計初期段階に徹底的に検討する「フロントローディング」が注目されています。主な目的は、後工程で発生しやすい設計の手戻りや問題点を未然に防ぎ、製品開発全体の効率化を図ることです。トヨタ自動車や川崎重工業、三菱電機といった大手企業の成功事例をもとに開発効率化やコスト削減を実現する手法を解説していきます。
フロントローディングとは?
フロントローディングは、製品開発において上流工程に重点を置き、初期段階で徹底して検討する手法です。後工程で発生しやすい設計の手戻りや問題点を未然に防ぎ、製品開発全体の効率化を図る目的があります。この章では、フロントローディングの具体的な意味やメリットについて、詳しく解説していきます。
フロントローディングの意味
フロントローディングとは、製品開発の上流工程における前倒しの検討強化であり、問題点を早期に検出し後工程での手戻りを防ぐ手法です。
製品開発では、後工程で設計変更が必要になったり、問題が発生したりすると、時間とコストの増大に繋がります。フロントローディングを用いて、開発の上流工程で検討を強化することで、開発期間の短縮やコスト削減が可能です。
フロントローディングを実現するための、具体的な活動は以下になります。
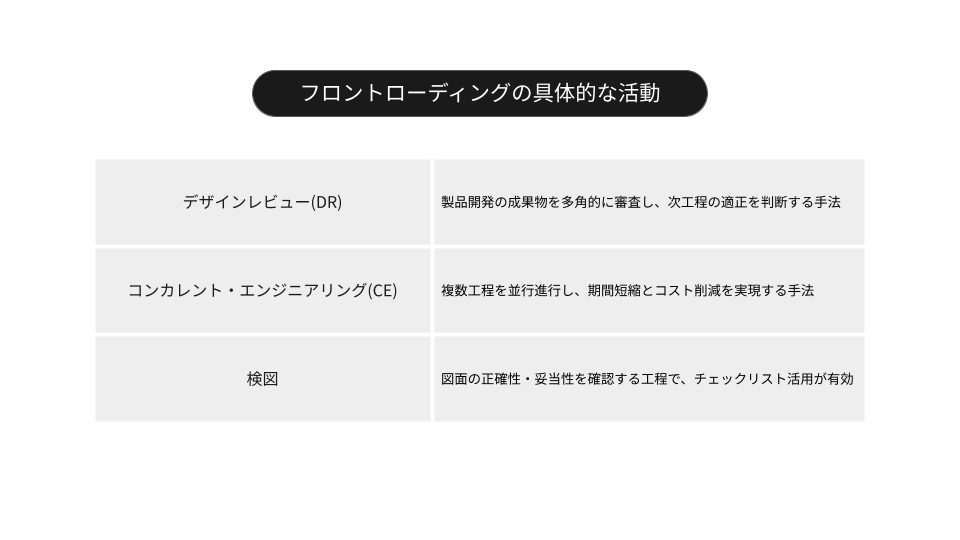
①デザインレビュー(DR)
「ISOナビ」によると、DRは、製品開発プロセスの各段階で仕様書や図面などの成果物を設計部門以外の人も含めて審査し、次のプロセスに進んで良いか判断する活動です。機能、性能、安全性、コスト、納期などの観点から妥当性を評価し問題点を抽出します。ISO9001の規定に基づく活動として製造業で広く活用されている手法の一つです。
②コンカレント・エンジニアリング(CE)
「KEYENCE」によると、CEは、製品開発の複数の工程を同時並行で進める手法で、開発期間を短縮してコストを削減できます。従来のウォーターフォール型開発に対し、CEは各工程を並行して進め、効率的な開発が可能です。特に設計初期段階でのリソース投入と部門間の情報交換が重要で、フロントローディングと組み合わせることで製品の品質向上も期待できます。
〈関連記事〉
コンカレントエンジニアリングとは?取り組みの全体像と事例について紹介
③検図
「ものづくりウェブ」によると、検図は設計図面の正確性と妥当性を確認する重要なプロセスで、主な目的は以下の通りです。
・図面がJIS機械製図のルールに従っているか確認する
・機能、性能、強度など設計上の問題がないか審査する
検図は、社外や部外への正式な図面提出やDRの前に実施され、不安な箇所があれば随時アドバイスを求めます。確認項目を抜け漏れなくするためにチェックリストの活用が有効です。後から修正する際に、具体的な指摘箇所がわかるように細かく不備内容を記録しておきましょう。
フロントローディングのメリットと重要性とは
フロントローディングは、製品開発の初期段階に検討を集中させることで、コスト競争力の強化、品質向上、開発リードタイムの短縮が可能です。グローバル競争が激化する中でフロントローディングの重要性が増しています。この手法が重要視される理由は、製品開発においてコストの8割が企画から製品設計段階で決まるためです。
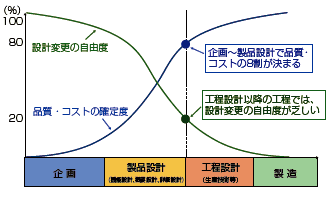
従来の開発プロセスでは、初期段階でコストや製造のしやすさ、安定供給といった要素が十分考慮されないことが多く、後工程で問題が発覚し手戻りが発生するケースが見られました。工程設計以降のプロセスになると設計変更の自由度が乏しく、最終的に開発期間が延びたり、コスト競争力を欠いた状態で量産が開始されたりするリスクがあります。
そんなリスクを低減できるフロントローディングを導入するメリットは、以下の通りです。
①コスト競争力の強化
初期段階でコスト要因を詳細に検討することで、量産後のコスト削減ができる。
②品質の向上
開発初期に設計の問題点を発見・修正することで、製品品質の向上が期待できる。
③開発リードタイムの短縮
手戻りを最小化し、全体のプロセスを効率化することで、市場投入までの期間を短縮できる。
近年では海外メーカーとの競合が激化しており、より低コストで高品質な製品を迅速に市場へ提供する能力が競争力の鍵となります。また、消費者ニーズの多様化と変化に対応すべく、開発スピードと柔軟性が必要です。フロントローディングを用いて、初期段階で徹底した検討をすることで、企業は市場での優位性を確保しやすくなります。
製造業でのフロントローディング実現に向けたポイント
製造業においてフロントローディングを実現するためには、従来の開発プロセスを見直し、効率的な情報共有と問題解決の仕組みを整備することが重要です。この章では、部門間の連携強化とシステムの活用という2つの観点から、具体的な取り組みについて説明します。
部門間連携の強化
製造業におけるフロントローディングを実現するには、開発の初期段階から部門間の連携を強化し、情報共有を効率的に行うことが重要です。
フロントローディングでは、設計やコスト、製造性などを早期に検討する必要があります。これを成功させるには、設計、製造、品質管理、調達といった各部門の密接な連携が重要です。従来のプロセスでは、部門間の連携が弱く、各部門が独立して作業を進めていたので、情報の断絶や手戻りが発生する課題がありました。
並行開発の推進
コンカレント・エンジニアリング(CE)を採用することで、各部門が開発初期から協働し、問題を早期に発見・解決できます。これにより、開発期間の短縮とコスト削減が可能になります。
共通プラットフォームの利用
デジタルツールやソフトウェアを活用して、各部門が同じデータをリアルタイムで共有し、意見を反映しやすくする仕組みを構築します。これにより、コミュニケーションの効率化が実現可能です。
部門間の定期的なレビュー会議
開発プロセスの重要な節目ごとに、全関係者が参加するレビュー会議を設け、全員の視点からリスクや改善点を洗い出します。
部門間の連携を強化することは、フロントローディングを成功させる上で不可欠です。このアプローチは、競争力のある製品を迅速に市場へ提供するための重要な考え方になります。
システム利用を通じた情報の蓄積と活用
製造業におけるフロントローディングを実現するためには、デジタルシステムを活用して情報を蓄積し、それを設計や意思決定に役立てることが大切です。
フロントローディングでは、設計段階で発生する情報を効率的に収集し、それを過去のデータや知見と結びつけることが求められます。従来の手法では、情報が個別のファイルや部門に散在しており、効果的な活用が難しいケースが多く見られました。
具体的な活用事例は以下の通りです。
PLM(Product Lifecycle Management)の導入
製品のライフサイクル全体を管理するシステムを導入することで、設計、製造、品質のデータを一元管理し、必要な情報を迅速に取得可能にします。
デジタルツイン技術の活用
仮想空間で製品のデジタルモデルを作成し、設計段階で製造可能性やコスト影響をシミュレーションすることで、より正確な意思決定ができます。
ナレッジデータベースの構築
過去の設計や生産データを蓄積し、類似案件への活用を可能にすることで、設計の精度向上と問題発生リスクの低減を図ります。
システムを通じた効率的な情報管理により、設計の精度とスピードを向上させ、競争力のある製品開発を可能にします。この取り組みは、迅速かつ的確な意思決定をサポートし、企業全体の開発力を強化する重要な役割のひとつです。
フロントローディングに調達購買部門が貢献するための開発購買
フロントローディングを製造業で実現するためには、調達購買部門が設計段階から積極的に関与し、製品開発プロセスを支援する体制が必要です。調達購買部門が設計部門やサプライヤーと協力し、早期段階から最適な調達計画やコスト管理を行う「開発購買」の取り組みが求められます。この章では、開発購買の意味や目的、そしてその重要性について詳しく解説します。
開発購買の意味
書籍「原価企画と開発購買戦略」によると、開発購買とは、調達・購買部門が設計部門と連携し、新製品の開発設計目標を達成するために取り組む活動になります。
この活動の目的は、設計段階からサプライヤーや材料選定に関する情報を活用し、製品のコスト、品質、製造性を最適化することです。設計部門だけでは考慮しきれない調達可能性や市場トレンドを取り入れ、効率的かつ効果的な開発が可能となります。
製品開発活動の支援
製品の企画や設計準備、製造初期管理の段階から調達購買部門が参加することで、開発工程全体を通じたサポートを実現します。
部門連携の強化
調達購買部門が設計部門だけでなく、サプライヤーや生産部門とも協働し、全体最適を目指します。
新たな価値の創出
サプライヤーとの協働を通じて新技術や新素材の提案を設計段階に取り入れ、革新的な製品開発に貢献します。
開発購買は、新製品開発における調達購買部門の役割を明確にし、設計部門やサプライヤーとの連携を通じて目標達成をサポートします。この取り組みは、競争力ある製品を効率的に市場へ提供するための重要な活動です。
開発購買の目的
開発購買の目的は、調達購買部門が設計部門と連携し、新製品開発における課題解決や目標値を達成することです。さらには製品設計目標の達成を通じて、効率的かつ競争力のある製品の実現を目指します。
開発購買の目的は3段階に分けられ、調達購買部門が段階的に目標を達成することで、新製品のコスト、品質、性能、納期などの多面的な要求に応えられるようになります。各段階は以下の通りです。
第1段階: 特定の課題解決目的
この段階では、開発設計過程で発生した特定の技術・性能・品質などの問題解決が目的です。具体的には、技術的課題を解消するための材料調達やサプライヤーとの協力が含まれます。
第2段階: 目標原価の達成目的
第1段階を含む形で、製造原価や物流コスト、さらには顧客の手元に渡るまでのコスト(TCO: Total Cost of Ownership)を考慮し、目標原価の達成を目指します。この段階では、初期の設計やサプライチェーン構築におけるコスト削減策が主な焦点です。
第3段階: 開発設計目標の達成目的
最終段階では、製品全体の設計目標を達成することが目的です。この目標には、特定の技術・性能・品質などの課題解決に加え、長期的な視点で市場のニーズに応えるための付加価値を創出する活動が含まれます。
これらの開発購買の目的を段階的に達成することで、競争力のある製品を市場投入するサポート体制が整います。
開発購買の重要性
開発購買は、製品の企画から設計段階でのコストや生産性、安定供給を最適化するために不可欠な活動です。特に海外競争や多様なニーズへの対応が求められる現代では、その重要性が増しています。
開発購買が重要である理由は以下の3つです。
- コストの8割は企画〜製品設計段階で決定
上流工程での設計によって、材料や製造工程、調達先の方向性がほぼ固まります。後工程では調達部門が努力してもコスト削減の余地が限られるため、調達部門が早期から関与し、調達視点を取り入れた最適な設計に導くことが重要です。これにより、効率的なコスト管理と製品競争力の強化を実現することが可能になります。
- コストの8割は企画〜製品設計段階で決定
- 従来のプロセスにおける問題点
企画・設計段階でコストや製造のしやすさ、安定供給について十分に考慮されていないケースが多く、後工程での問題発覚が一般的でした。これにより、設計変更が発生し、開発リードタイムの延長や、コスト競争力の低い状態での量産開始につながることが課題になります。
- 従来のプロセスにおける問題点
3.日本メーカーの市場シェアが近年低下傾向
上図の通り、日本企業の国際競争力はこの10年で低下していることが分かります。特に北米企業と比較すると、競争力の差は約2.5倍となり深刻な状況です。
これ以上市場シェアの低下を食い止めるためにも、初期段階での調達購買活動を強化し、競争力を維持する必要があります。特に初期段階でのコスト最適化や製造性の向上が競争力を高めるポイントです。
海外企業との競争や消費者ニーズの変化に対応するためにも、調達購買部門が設計部門と連携し、効率的な開発プロセスのサポートが求められます。
〈関連記事〉
フロントローディングの製造業の事例
フロントローディングは、多くの製造業で導入され、開発プロセスの効率化やコスト削減、品質向上を実現する手法として活用されています。企業ごとに異なるアプローチや技術が導入されており、その成功事例は他業界への展開が可能です。この章では、具体的な事例としてトヨタ自動車、川崎重工業、三菱電機の取り組みについて詳しく説明します。
トヨタ自動車の事例
トヨタ自動車の事例では、「サイマルテニアス・エンジニアリング(SE)」と呼ばれる、製品開発プロセスを効率化し、品質向上とコスト削減を同時に実現する手法を採用しています。この手法は、製品企画から量産仕様決定プロセス間で、生産部門の製造部や生産技術、外注先などを巻き込むことで、設計品質の最適化と量産時の問題を最小化している事例です。
従来の製品開発では、設計と生産準備が分離しており、後工程での問題発覚が一般的でした。トヨタのSEでは、生産部門や外注先が設計初期段階から参画することで、以下のメリットを得られます。
・設計変更の最小化
開発段階で設計変更や改良を徹底し、量産時の変更を最小限に抑える。
・戦略的な原価低減活動の実現
関係者全員に目標を設定し、誰もが改善提案を行える体制を構築する。
・外注仕入先との協力関係の構築
外注先と協力し、品質問題の抑制やロスの削減を実現する。
・開発費の低減とリードタイムの短縮
試作を省略する「試作レス」開発モデルを採用し、開発費用と期間を大幅に削減する。
・複数生産拠点での同時生産立上げ
国内外の製造条件を考慮し、図面仕様に反映することで、同時生産と市場開拓を可能にする
トヨタのSEは、フロントローディングの具体例として、開発初期からの部門横断的な取り組みによってコスト削減、品質向上、リードタイム短縮を同時に実現しました。このモデルは他業界にも適用可能であり、競争力強化の重要な手法になります
川崎重工業の事例
川崎重工業の事例では、フロントローディング手法を活用したWMATA7000プロジェクトに取り組む内容になります。設計初期段階からリソースを集中投入し、短納期・高品質の鉄道車両を効率的に開発・生産した成功事例です。
鉄道車両の設計では、既存設備との適合や短納期、高度な性能要件への対応が求められます。フロントローディングを用いて初期段階で課題を洗い出し、解決策を反映することでプロセス全体の効率化を実現しました。
このプロジェクトでのフロントローディングの具体的な取り組みは、以下の通りです。
- 設計リソースの集中投入
プロジェクト初期から設計・技術部門や外部機器メーカーが協働し、早期に設計を確定。軽量化や耐衝突性の向上、空調システムを最適化。
- 設計リソースの集中投入
- シミュレーション技術の活用
数値流体力学(CFD)や統計的エネルギー解析(SEA)を駆使して、空調ダクトや車内騒音、台車性能を事前に最適化し、手戻り防止を実現。
- シミュレーション技術の活用
- コンカレントエンジニアリングの採用
設計と生産計画を並行して進めることで、製造の実現可能性を設計段階から考慮。薄型床構造や車体強度の検討の効率化に成功。
- コンカレントエンジニアリングの採用
- 新技術の採用
新素材や新構造を積極的に導入し、剛性と軽量化を両立。運転室設計では3Dモデリングを用いて操作性や視認性を向上。
- 新技術の採用
フロントローディングを用いたWMATA7000プロジェクトは、設計初期段階からの全体最適化を可能にし、手戻り削減と開発期間の短縮を実現した事例のひとつになります。
三菱電機の事例
フロントローディング型熱設計を採用した三菱電機の事例では、設計初期段階で熱問題を予測・解決し、設計品質向上、開発費削減、開発期間短縮を実現する手法です。
従来の「火消し型」熱対策では後工程での問題発生が多く、コストや時間が増大していました。三菱電機のフロントローディングでは、STEP1で初期検討、STEP2で詳細なシミュレーションを行うことで、設計不具合を未然に防ぎます。
具体的な事例は以下の通りです。
- LED-DLP方式リアプロジェクタシステム
– STEP1:熱経路を簡易化し、ヒートシンク設計を表計算で最適化。
– STEP2:三次元熱流体解析で風路設計と部品配置を検証し、温度管理を実現。
- 薄型液晶テレビ(BHRシリーズ)
– STEP1:自然空冷での排熱量を簡易計算ツールで確認。
– STEP2:熱流体解析を行い、HDDの温度上昇を煙突効果で抑制し、対策不要で基準クリア。
フロントローディング型熱設計は、設計フェーズごとに段階的に検討し、効率的な問題解決と市場投入の迅速化を実現します。これにより、品質(Q)、コスト(C)、納期(D)の改善が可能となり、競争力強化への貢献度が高いです。
まとめ
フロントローディングは、製品開発の初期段階で課題を徹底的に洗い出し、後工程の手戻りを防ぐことで品質向上やコスト削減、開発期間の短縮を実現する手法です。トヨタ自動車や川崎重工業、三菱電機の事例からも分かるように、部門間連携やデジタル技術の活用が成功の鍵となります。これにより、競争力の高い製品開発と市場投入のスピードを大幅に向上させられるでしょう。
投稿者プロフィール
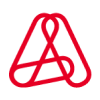
- A1A編集部
- A1Aブログは製造業向け調達データプラットフォーム「UPCYCLE」を提供するA1A株式会社が運営するメディアです。製造業の調達購買業務に役立つ情報を発信しています。
最新の投稿
2025年6月17日RFQとは?RFI・RFPとの違いを解説 ダウンロード可能なExcelテンプレート付き
2025年6月12日集中購買とは?実践方法や分散購買との使い分け、メリット・デメリットを紹介
原価低減2025年5月26日原価低減とは?購買・調達部門がコストダウン成果を出すための考え方と手法を紹介
2025年5月13日納期遵守率の計算式と調達部門における納期遵守率の改善のポイントとは