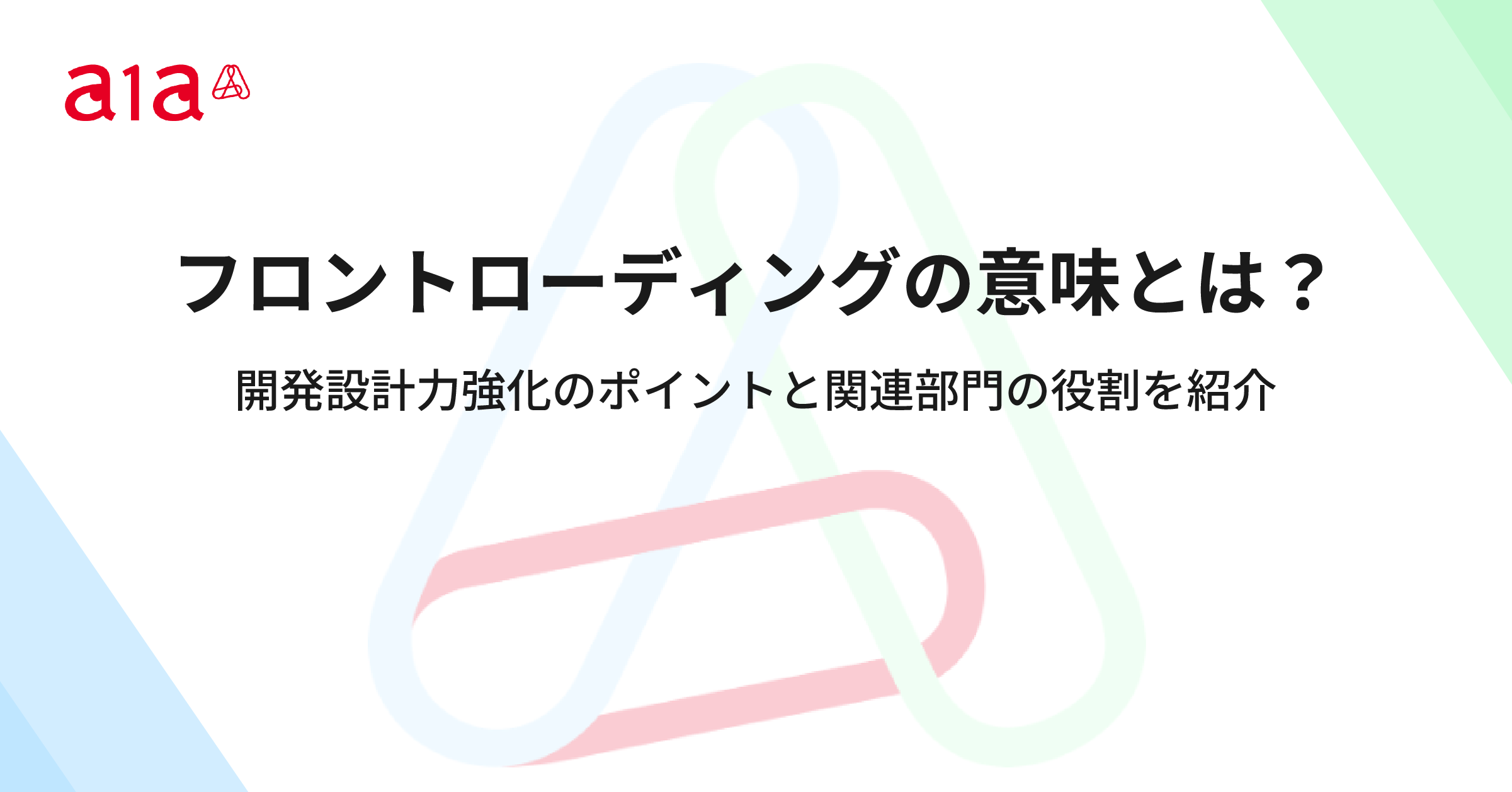
新製品をタイムリーに市場に投入し、コスト削減も求められている昨今では、フロントローディングという手法が注目されています。製品開発に取り組む際にフロントローディングを導入すれば、後戻りを防げるため開発リードタイムの短縮につながるばかりか、最適な材料や部品を早期に決定できることによって、コスト低減にもつながるからです。
しかし、フロントローディングは設計にかかわるものであることから、特に調達購買部門の人にとってはなじみがないかもしれません。
そこで本記事ではフロントローディングの意味やメリットといった基本的なこと、調達購買部門をはじめとする各部門の役割、実現するポイントなどを分かりやすく解説します。
フロントローディングとは
ここではフロントローディングの意味とメリット、そして重要性について解説します。
フロントローディングの意味
フロントローディングとは、製品開発の上流工程において前倒しで作業を行い、設計の効率化や品質向上を図るアプローチ手法です。
一般的な製品開発のプロセスは、企画構想→基本設計→詳細設計→試作→量産、となります。設計のみで完成度の高い製品を開発するのは難しく、時には量産段階に入ってから設計変更が発生する場合も珍しくありません。しかし、フロントローディングでは設計フェーズの早い段階にリソースを投入し、仕様や設計などを深く検討します。従来の方法より上流工程の作業負荷は高まりますが、設計の精度を確保でき、量産になってからの後戻りも少なくなります。
フロントローディングは以下の3つの活動を通して行います。
・デザインレビュー
・コンカレントエンジニアリング
・検図
デザインレビューとは設計審査のことです。図面や試作品を通して「仕様や設計に不備がないか」を複数人で評価し、改善を施します。通常は基本設計フェーズ、詳細設計フェーズ、試作フェーズと、節目ごとに行われます。
コンカレントエンジニアリングは、製品づくりにかかわる様々な部門が業務を並行して製品開発に取り組む手法です。特に生産技術や調達購買、原価企画、製造といった人々が設計検証に参加して知恵を持ち寄ることで、量産に取りかかるスピードを早めることができます。たとえば製造部門の視点から、組み立てやすい形状を設計にフィードバックするといったことが想定されます。
最後の検図とは、文字通り図面のチェックです。「強度に問題はないか」「寸法精度は正しいか」など、設計的に問題はないかをチェックするのはもちろん、図面がルールどおりに書かれているかも重要なポイントです。JISのルール通りに記載がされていないと、外部の加工業者が図面を見てもどう加工してよいか分からず、手戻りや品質不良が発生してしまうからです。
フロントローディングのメリット
フロントローディングのメリットは3つあります。
1つ目は「コスト低減」です。製品開発のプロセスは下図の通り、上流にあるほど設計の自由度は高く、見直しもしやすくなります。したがって設計フェーズで検討を深めると、強度的に過剰品質といえる材料を見直したり、部品の標準化を推し進めることで部品点数を減らしたりと、製品コストを低減することが可能です。
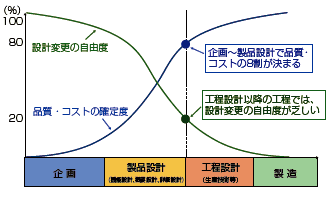
フロントローディングは製品開発の後工程にも良い影響がもたらされます。たとえば生産において加工しやすい形状や材質にすることで、生産性が向上するため、全体的なコストは削減されるからです。このようなコスト競争力の強化はフロントローディングのメリットと言えます。
2つ目は「品質の向上」です。フロントローディングでは設計の早い段階でシミュレーターを駆使しながら検証を行うことになります。少しでも深くまで検討し、得られた確かなデータから設計の精度を高めることができるのです。したがって、量産段階で製品に思わぬ不具合が生じ、不良品が頻発するような事態を防ぐことができます。
3つ目は「開発リードタイムの短縮」です。開発プロセスにおいて懸念されるのは、試作段階や量産に至って、顧客の要求する仕様が正しく反映されていなかったり、設計にミスがあったりなどが発見されることです。
後工程になってこのような不備が見つかると、設計をやり直す必要があり、製品開発に多大な時間がかかることになります。しかし、設計フェーズで深くまで検証を繰り返しているフロントローディングでは、後戻りが少なくなり、全体的なリードタイムを少なくできます。
フロントローディングの重要性
基本的にモノづくりは設計で決まった通りの材料を調達し、図面に書かれてある通りに加工・組み立てを行います。工程設計や製造において設計変更を行うことは少なく、コストの8割は企画〜製品の設計段階で決まってしまうと言われます。そのため、企業としては開発の初期段階にリソースを集中的に投入してでも、製品原価の見直しをする必要があるのです。
また、従来の製品開発には問題点が潜んでいることも事実です。従来通りに設計部門だけで開発を進めていくと、製造の段階で加工や組み立てのしにくい図面が出来上がったりします。この段階で設計変更をするのは容易ではないため、仕方なく余分な手間をかけて製造を行うことになりかねません。フロントローディングにおいて各部門が参加し、シミュレーションを繰り返していればそのような事態も防げるでしょう。
とはいえ、フロントローディングには設計部門の負担がかかり、初期投資も必要など、少なからぬデメリットもあります。それでもなお、フロントローディングに取り組むべき理由とはなんでしょうか。
それはメーカーを取り巻く環境が目まぐるしく変化しているからです。ひと昔前の大量生産の時代は終わり、顧客の求める仕様に合わせて多品種少量生産を行うことが求められています。さらにグローバル化も進み、海外メーカーとの熾烈な争いにも巻き込まれており、下図のように日系企業の競争力は低下してきているのが現状です。
そのため、新製品をタイムリーに投入するために開発リードタイムを短縮し、海外メーカーと競争できるようにコスト競争力を強化する必要があるのです。
フロントローディング活動に関連する各部門の役割とは
フロントローディングでは各部門が連携してチームワークを発揮することが大切です。ここでは開発・設計部門、原価企画部門、調達購買部門のあるべき役割について解説します。
開発・設計部門の役割
先述の通り、従来の製品開発プロセスは後戻りが大きな課題でした。それを防ぐ一つの方法は、設計検証の前倒しです。
設計フェーズが基本設計→詳細設計→試作→単体試験→組み合わせ試験→総合検証だった場合、従来通りにいけば一つ一つのプロセスが終わった段階でバトンタッチのように次のプロセスに移ります。しかし、設計内容の検証を試作品や実機を使うとなれば、製作するまでに時間がかかります。さらに、検証フェーズで設計の間違いや性能が不十分だということが分かれば、基本設計や詳細設計に戻って修正対応をしなければなりません。
そこで設計検証の前倒し、つまり設計フェーズにおいてシミュレーションソフトを活用し、設計と並行して検証を行うことで、製作作業や後戻りの発生を無くすことができます。メカとエレキ、ソフトを設計する場合には、3つを並行して開発するといった方法が考えられるでしょう。
フロントローディングにおいては、設計部門の負荷が高まりがちです。ただし、製品開発プロセスは、部分最適ではなく全体最適の視点が大切になります。設計などの上流工程の作業負荷が高まる代わりに後工程の効率化が図れ、全体最適につながるのであればフロントローディングに取り組む価値はあります。
原価企画部門の役割
フロントローディングにおいて、原価企画部門は全部門を巻き込んで目標原価を達成するという役割があります。設計までに原価の8割が決まってしまうと言われる製品開発では、量産フェーズに入ってしまうと原価低減を狙うのは難しくなります。したがって、企画の段階で利益を確保できるように目標原価の作りこみを行うことが大切です。
ただし、設計や生産部門は品質や納期を優先しがちであるため、原価低減を狙う場合に利害対立が発生しやすくなります。そこで原価企画部門が各部門の利害関係を調整しながら、全体最適という視点から原価の作りこみを推進します。
とはいえ、原価低減はいきなりできるものではありません。日頃から情報を収集し、過去の経験なども組み合わせながら最適なアイデアを導き出すためには、データを蓄積し活用することが必要です。
蓄積したデータを活用していけば、加工などによりどのくらいの原価がかかるのか、見積もることが可能になります。たとえば金属加工であれば、材料の種類、材料質量、材料単価、サイズ、加工条件などを決めた設計段階で、原価を正確に見積もることができれば目標原価の達成率も導き出すことができるはずです。このような見積もりができる仕組みを原価企画部門として確立する必要があります。
調達購買部門の役割
調達購買部門の役割は材料をただ安く調達するだけではありません。フロントローディングにおいては製品開発の上流工程で、設計の改良の提案、材料の価格査定、サプライヤーとの交渉などが求められています。購買部門が上流工程から開発に携わることを「開発購買」と呼びます。
開発購買を実現するための条件は以下の3つです。
1つ目は、設計の意図を理解しながら調達部材に対するコストダウン策やVE提案ができることです。部品の共通化や製造方法、形状、寸法精度などさまざまな視点から品質を保ちながら、今よりもコスト低減ができないか提案できる能力が必要とされます。
2つ目は、設計段階におけるアイデアに対してすぐに価格査定ができることです。調達品の原価明細情報のデータベースを活用することで、上流段階における精度の高いコストの概算見積を実施することができれば、フロントローディングがよりスムーズになります。
3つ目は、サプライヤーと目標原価を達成できるように交渉できることです。サプライヤーに対して仕入価格を下げることばかり要求するのが良いわけではありません。両者が共存共栄するために、優れたVE提案をサプライヤーから引き出すのも調達購買部門の役割です。
また、サプライヤーは国内ばかりではありません。グローバル化の今では海外のサプライヤーとの交渉も視野に入れて、サプライヤー候補をリストアップしておくことが大切です。技術は日進月歩で進化しています。調達購買部門はサプライヤー市場を分析し、設計者に最新技術のトレンドを紹介できるまでにリサーチする能力が求められているのです。
フロントローディング実現に向けたポイントとは
フロントローディング実現に向けては以下の3つの観点から行うことがポイントになります。
社内における目的意識の合意
フロントローディングを実行する時には社内で「なぜフロントローディングなのか」という目的を共有することが大切です。そのためには、現状の損失の可視化と開発リードタイム短縮の効果の算出といった定量化が非常に大切です。
損失の定量化には以下のようなものがあります。
・手戻りのコスト:設計変更や仕様変更による再作業のコストを算出します。
・遅延によるペナルティ:納期遅延による契約上のペナルティや機会損失を計算します。
・品質問題の影響:不具合修正や顧客サポートにかかるコストを見積もります。
これらに加えてフロントローディングによって期待される効果を具体的な数字で示すことが重要です。まず、初期段階での綿密な計画と準備により、全体の開発期間がどの程度短縮されるかを予測します。次に手戻りの減少や効率化によるコスト削減効果を算出し、品質向上によって生じる不良率の減少などを算出します。
現状の損失と想定される改善効果を直接比較することで、フロントローディングの導入によるメリットを明確に示すことができるのです。これにより社内でフロントローディングに取り組む意味を定量的に掴むことができ、目的意識の合意に役立ちます。
部門間連携の強化
フロントローディングは設計部門だけでなく、生産技術や原価企画、調達購買、生産部門といったさまざまな部門が関わらなければ実現できません。プロジェクトと同じような考えのもとに、関連部署のコアメンバーを招集するなどして、組織的に運用できる体制を整えることが大切です。
プロジェクトを推進するためにはまずリーダーを選出しなければなりません。リーダーには企画から開発、設計、製造、保守、廃棄までのエンジニアリングチェーンと、原料調達、製造、物流、販売までのサプライチェーンの両方を熟知した人材が必要になります。なぜなら開発設計だけでなく、組立加工や保守、回収処理といった製品ライフサイクル全体の視点からフロントローディングに取り組むことが重要となるからです。したがってリーダーにはある程度の経営資源を動かす権限を持ち、製品開発プロセスに知見のある人が適任となります。
業務プロセスに精通している人材も必要であるため、必要に応じて生産技術や生産部門からサブリーダーを選出するとよいでしょう。全体のリーダーをもとに、各部門から実務を担当するメンバーを選出することになります。各部門から必要なスキルを持ち、フロントローディングを実行できるだけのポテンシャルを持った人材が欠かせません。
システム利用を通じた情報の蓄積と活用
後戻りを防ぎ、開発リードタイムを短縮する効果のあるフロントローディングでは、設計段階で検証を前倒しすることが大切です。そのためには試作機ではなく仮想的にシミュレーションをするための3DCADやCAEなどのシステムを活用することが必須になります。
たとえばメカ・エレキ・ソフトで構成される製品の場合には、メカとエレキの設計を待ってからソフト開発に取り組むことが一般的です。しかしタイムリーに製品を販売していくためにはメカ・エレキの開発を待ってからソフト開発に取りかかるとリードタイムが長くなりがちです。そこでメカ・エレキ部分を仮想的にモデル化し、仮想装置をもとにソフト開発を行うといった活用法もあります。これによりメカやエレキが完成する前に、ソフト開発の大部分を仕上げることが可能になります。
また、調達購買に関するデータも蓄積することが大切です。サプライヤー市場を分析する資料では、「市場規模、市場をリードしている地域・企業はどこか」「デファクトスタンダードは何か」などを取り揃えておきます。VEに関するアイデアも蓄積しておくと、たたき台になります。形状、寸法精度、材質、製造方法、標準化などの視点からアイデアやノウハウを蓄積できるとよいでしょう。
フロントローディング実現に効果的なツール
フロントローディングではシステムの活用が欠かせません。ここでは効果的なツールを紹介します。
3D CAD
3D CADとは、立体データで設計ができる設計支援ソフトのことです。図面には2次元図面と3次元図面の2種類があり、通常、複雑な形状の設計物には3D CADを使用し、各部品の加工指示などは2次元の図面を使用します。
3D CADのメリットは部品点数が多く、複雑な形状の設計図でも立体的に細かく把握できる点です。特に組立品においては部品同士の干渉などを平面図で理解するのは難しく、実際に組み立ててから問題が発生することも珍しくありません。しかし、3D CADであればコンピューター上で部品の干渉から動作のシミュレーションなどが確認できるようになります。
3D CADは設計部門だけでなく、さまざまな部門で共有すべきです。なぜなら、図面を理解するのが難しい人でも3D CADであれば、感覚的に設計内容を理解できるからです。たとえば設計内容の検証を行う際に活用すれば、組み立て性の評価などの視点で生産部門や調達購買部門からアイデアを引き出すことが可能になります。
設計内容を変更する際にも3D CADならではのメリットがあります。部品を変更すると自動的に反映されるアセンブリ機能があるためです。設計変更が多くなりがちで、設計段階で負荷のかかるフロントローディングに向いているツールと言えます。
CAE
CAE(Computer Aided Engineering)は、コンピューター上で仮想の試作品を評価できるシステムです。CAEでは応力解析や振動解析といった構造解析、流体解析、熱伝導解析などが可能です。実際に試作品を製作しなくてもシミュレーションができるため、フロントローディングにおいては欠かせないツールとなります。
たとえば自動車の開発の場合、実際に試作車を作って衝突実験などを行うと、それだけのコストと時間がかかります。CAEでは仮想的に衝突実験のシミュレーションができるため、どのようなリスクがあるか、部品の強度はどうか、などの早期検証に役に立ちます。
CAEは設計者が部品の形状や寸法を決定するために使用することが多くなりますが、フロントローディングにおいてはさまざまな部門のアイデアや要望を早期の段階で反映できるというメリットがあります。
製造部門が作りやすさを主張するようであれば、設計段階で組み立てや加工のしやすい形状にすることができ量産に入ってからの後戻りを防ぐことができます。あるいは調達購買部門からの新素材の採用といったVE提案に対して材料力学の観点から、シミュレーションを通して最適な判断を下せるでしょう。
調達データプラットフォーム
調達データプラットフォームとは、調達品に関するコスト明細情報や図面情報が蓄積されたデータベースです。設計段階において、材料や形状を検討する際に、調達品のコスト情報を蓄積されたデータベースを用いることで、より最適な部材や形状、仕様、コストを検討することが可能になります。
先述のとおり、原価の8割は上流工程の企画開発や設計で決まってしまいます。したがって、上流工程で調達コストを深くまで検討し、原価の作りこみ、原価の低減が必要です。しかし、過去の調達品のコストに関する情報がデータ活用できる状態で蓄積されていないと、タイトなスケジュールの中でコストの概算の見積を算出したり、サプライヤーから受領した見積書の査定を精度高く行うことが難しくなります。
調達データプラットフォームは調達品のコストに関連する情報がデータベース化されているため、効率的かつ精度の高い設計アイディアの概算見積や見積査定、VE検討に役立ちます。
まとめ
フロントローディングは製品開発プロセスにおいて前倒しできる作業は企画~設計フェーズで行うというアプローチ方法です。
量産に取りかかる前の設計フェーズで検証を深くまで行えるため、製品開発のリードタイムが短縮できる、原価低減を達成できる、後戻りを防げるといったさまざまなメリットがあります。
フロントローディングではさまざまな部門が知恵を持ち寄ることが大切です。従来は図面通りに調達すれば良かったかもしれませんが、フロントローディングにおいては設計段階から積極的に参加して、材料の価格査定からVE提案ができる開発購買が求められているのです。
投稿者プロフィール
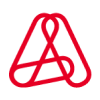
- A1A編集部
- A1Aブログは製造業向け調達データプラットフォーム「UPCYCLE」を提供するA1A株式会社が運営するメディアです。製造業の調達購買業務に役立つ情報を発信しています。
最新の投稿
2025年8月8日材料支給とは?メリットや注意点、有償支給・無償支給・管理自給の違いなどを解説
2025年7月28日コストエンジニアリングとは?進め方と手法についてわかりやすく解説
2025年6月17日RFQとは?RFI・RFPとの違いを解説 ダウンロード可能なExcelテンプレート付き
2025年6月12日集中購買とは?実践方法や分散購買との使い分け、メリット・デメリットを紹介