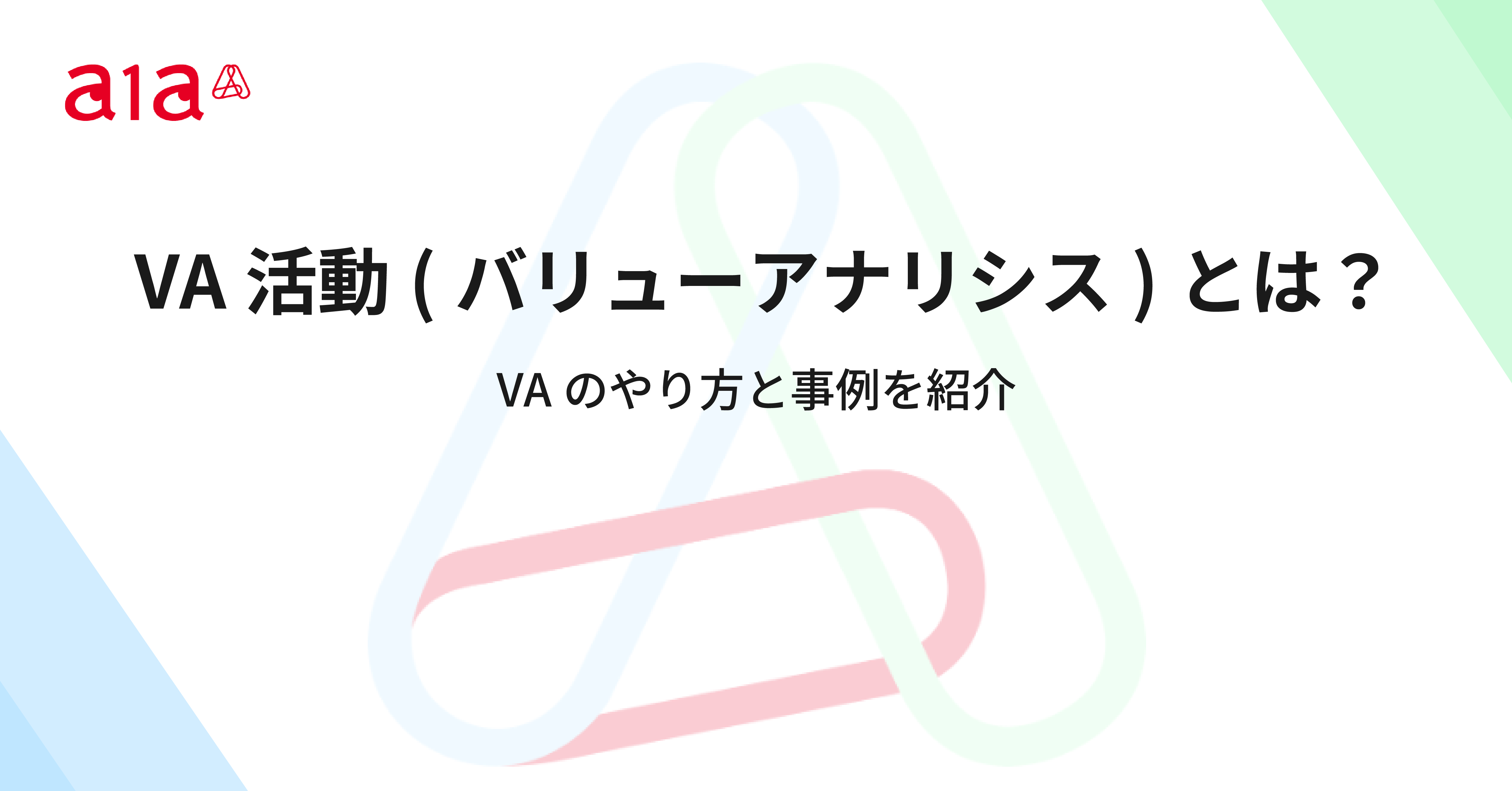
投稿者プロフィール
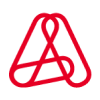
- A1Aブログは製造業向け調達データプラットフォーム「UPCYCLE」を提供するA1A株式会社が運営するメディアです。製造業の調達購買業務に役立つ情報を発信しています。
最新の投稿
2025年6月12日集中購買とは?実践方法や分散購買との使い分け、メリット・デメリットを紹介
原価低減2025年5月26日原価低減とは?購買・調達部門がコストダウン成果を出すための考え方と手法を紹介
2025年5月13日納期遵守率の計算式と調達部門における納期遵守率の改善のポイントとは
2025年5月7日調達購買部門向け 交渉力強化のポイントを解説