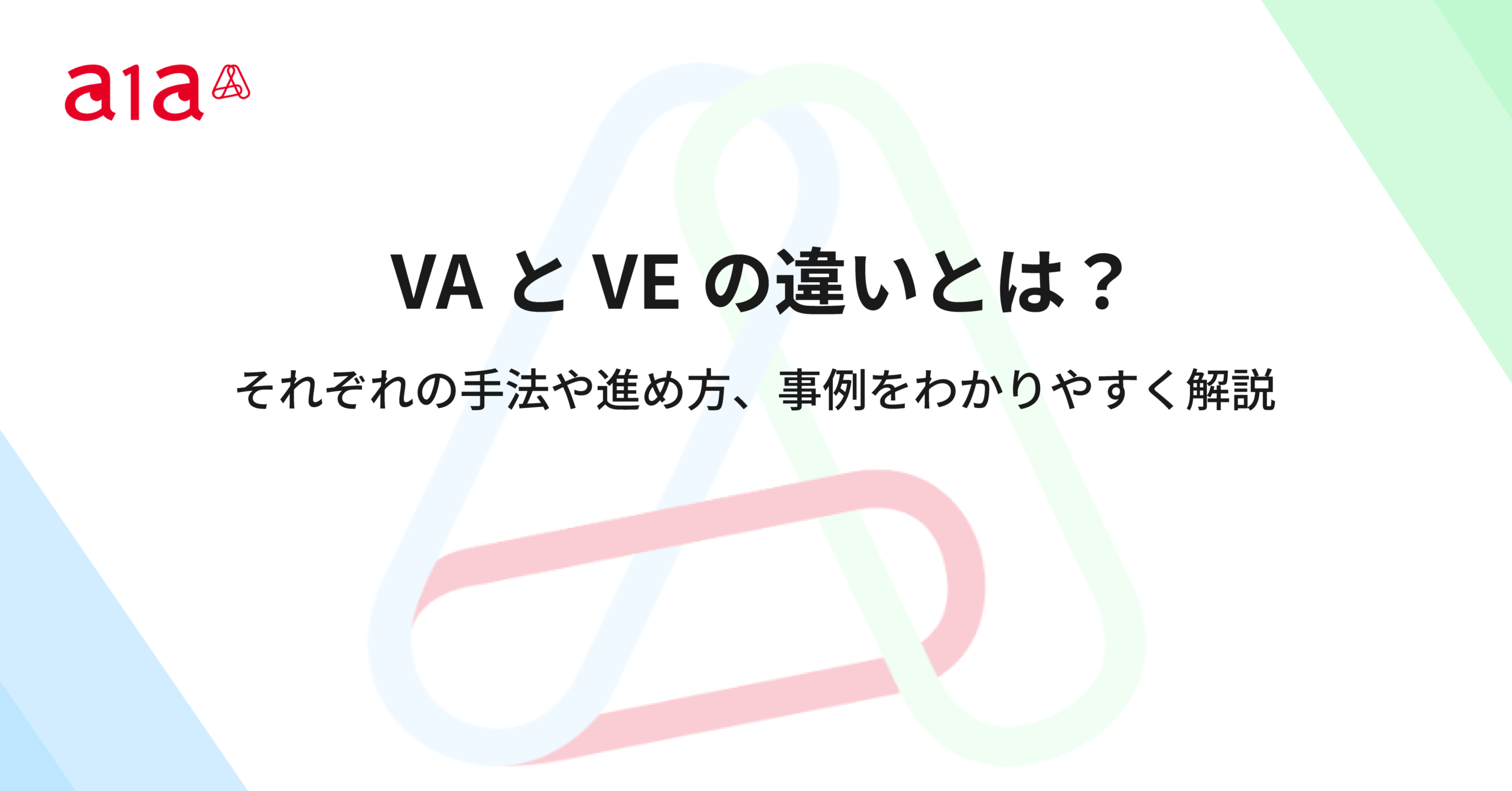
投稿者プロフィール
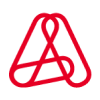
- A1Aブログは製造業向け調達データプラットフォーム「UPCYCLE」を提供するA1A株式会社が運営するメディアです。製造業の調達購買業務に役立つ情報を発信しています。
最新の投稿
2025年7月28日コストエンジニアリングとは?進め方と手法についてわかりやすく解説
2025年6月17日RFQとは?RFI・RFPとの違いを解説 ダウンロード可能なExcelテンプレート付き
2025年6月12日集中購買とは?実践方法や分散購買との使い分け、メリット・デメリットを紹介
原価低減2025年5月26日原価低減とは?購買・調達部門がコストダウン成果を出すための考え方と手法を紹介