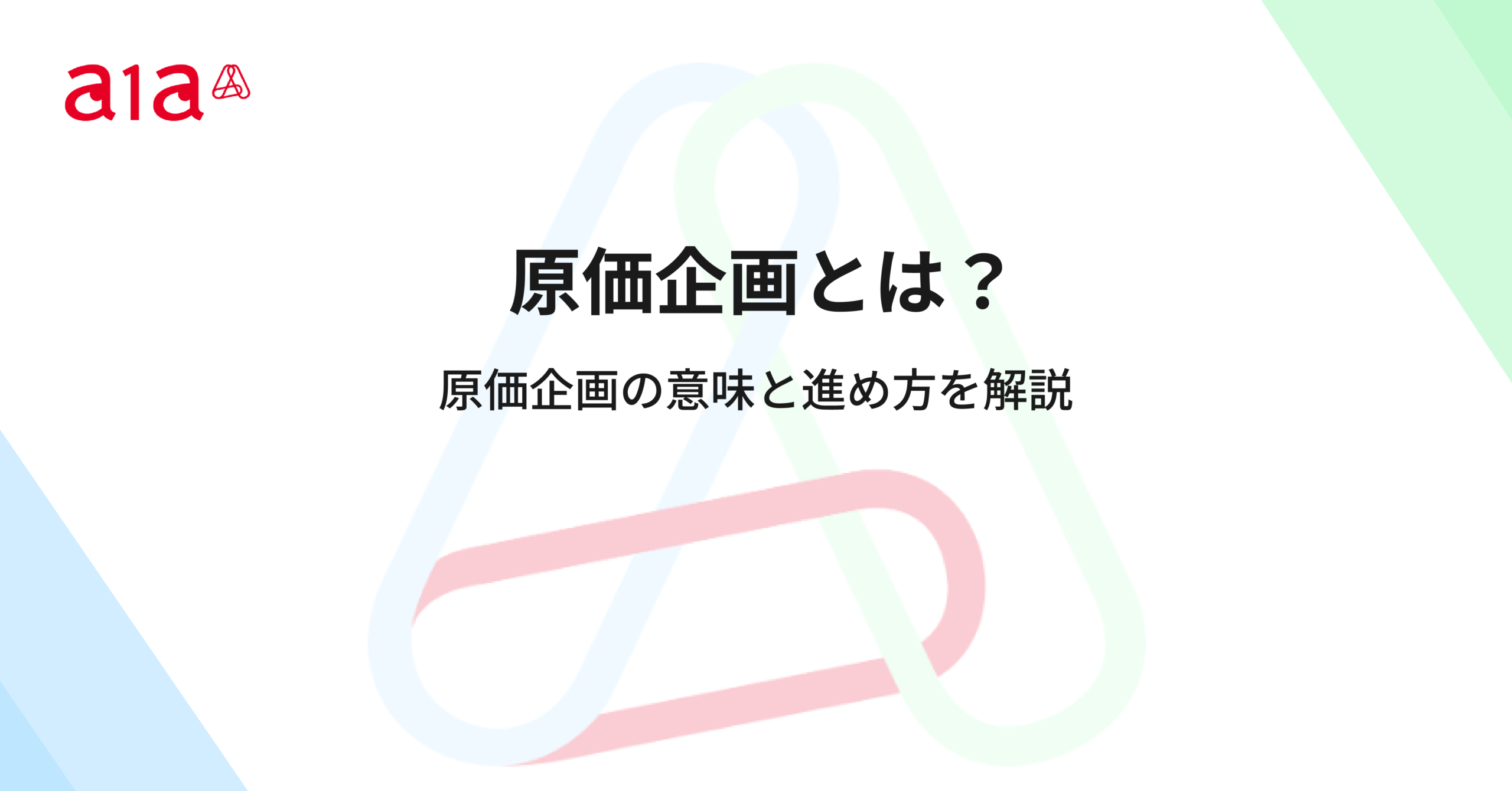
投稿者プロフィール
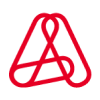
- A1Aブログは製造業向け調達データプラットフォーム「UPCYCLE」を提供するA1A株式会社が運営するメディアです。製造業の調達購買業務に役立つ情報を発信しています。
最新の投稿
2025年6月17日RFQとは?RFI・RFPとの違いを解説 ダウンロード可能なExcelテンプレート付き
2025年6月12日集中購買とは?実践方法や分散購買との使い分け、メリット・デメリットを紹介
原価低減2025年5月26日原価低減とは?購買・調達部門がコストダウン成果を出すための考え方と手法を紹介
2025年5月13日納期遵守率の計算式と調達部門における納期遵守率の改善のポイントとは